
Disalfarm consegue capacidade, produtividade e controle com a automatização em distintas fases do seu armazém convencional
Disalfarm automatiza seu armazém de forma simples e econômica com transelevadores trilaterais
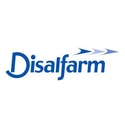
Este centro logístico localizado nas instalações que a Disalfarm possui em Rubí (Barcelona), foi edificado sobre uma superfície de 39.027 m². O armazém, totalmente automático atualmente e com uma capacidade de armazenamento para mais de 19.000 paletes, melhorou notavelmente a produtividade da empresa. Tudo isso, sem deixar de trabalhar em momento algum durante a ampliação e modernização do armazém.
Quem é a Disalfarm?
A Disalfarm S.A. é uma empresa de logística criada na Espanha pelos laboratórios Bayer, Boehringer Ingelheim e Novartis com o propósito de concentrar suas operações nacionais, tanto de armazenamento quanto de distribuição de especialidades farmacêuticas.
A empresa iniciou suas atividades no ano de 2000 com a ambição de ser uma empresa líder no setor da distribuição farmacêutica. Para consegui-lo, era indispensável trabalhar sob um sistema de qualidade que garantisse as normas de fabricação e distribuição exigidas pela legislação vigente.
A Disalfarm, hoje em dia, dispõe de uma ampla gama de produtos que abrange as especialidades farmacêuticas de prescrição médica, os medicamentos de uso hospitalar, de uso veterinário, os suplementos alimentares, além de outros produtos relacionados com a saúde.
Onde está localizada?
A Disalfarm, S.A. fica na cidade de Rubí, uma área industrial próxima de Barcelona que coincide com uma importante ligação rodoviária.
Suas instalações estão localizadas perto dos principais centros logísticos e de distribuição, o que lhe permite oferecer um serviço ágil e rápido a todos os seus clientes.
Necessidades da Disalfarm: melhorar sem reduzir o serviço
O crescimento registrado pela Disalfarm nestes últimos anos fez com que suas necessidades de armazenamento tenham aumentado substancialmente.
Em 2000 construiu um centro logístico que combinava as operações de armazenamento com as de picking – menos de 20% dos pedidos correspondiam a paletes completos de uma única referência.
Nesta primeira fase também foram criados dois galpões dedicados ao armazenamento, uma área de preparação e consolidação, as docas de carga e descarga e, por último, os escritórios e serviços.
O conjunto destas instalações ocupava uma superfície de 9.706 m2. Todas as estantes do armazém e a área de picking foram instaladas pela Mecalux.
Em 2007 o armazém propriamente dito ficou pequeno. O elevado número de movimentos realizado pelas empilhadeiras de movimentação representava um custo desmedido e, ao mesmo tempo, aumentava o risco de acidentes de trabalho, algo contrário aos princípios da Disalfarm.
Diante desta situação, o grande desafio que a empresa abordou junto à Mecalux foi atualizar este centro logístico sem ter que alterar o serviço proporcionado aos seus clientes.
Ponto de partida: fase 1 e fase 2
Na primeira fase, que ocorreu no ano de 2000, foi construído:
- Um armazém com capacidade para 12.900 paletes de 800 x 1.200 mm formado por dez corredores com estantes de 15 m de altura.
- Área de picking composta por estantes dinâmicas com dispositivos pick-to-light e transportadores de caixas que se encarregavam de fazer a ligação desta área com a de embalagem e consolidação.
- Área de picking de caixas completas cujo picking é feito diretamente sobre os paletes.
- Armazém para produtos refrigerados com capacidade para 290 paletes.
- Armazém fechado para produtos psicotrópicos.
- Nove docas de carga com uma ampla área de manobra.
Na segunda fase foram adicionados mais cinco corredores com estantes de paletização convencional com capacidade para 6.450 paletes, totalizando 19.350 paletes.
Além disso, foram finalizadas três novas docas de carga.
O fluxo de movimentos também aumentou consideravelmente alcançando 1.100 paletes por dia (500 de entrada e 600 de saída).
Para poder mover este número de paletes foram utilizados os seguintes recursos:
- Sete empilhadeiras de carga frontal para trabalhar nas docas, alimentar as áreas de picking, assim como depositar e retirar os paletes da cabeceira dos corredores.
- Cinco empilhadeiras trilaterais para trabalhar unicamente no interior dos corredores de armazenamento.
- 24 operadores para manusear as empilhadeiras (12 por turno).
Nos dois gráficos exibidos nesta seção podemos observar como os fluxos de movimentos (entradas e saídas) se cruzam no corredor principal.
Fluxo da mercadoria nas fases 1 e 2
A mercadoria chegava ao armazém completamente paletizada. O operador fazia a leitura do código de barras de cada palete com um terminal informático e o sistema de gestão do armazém (SGA) lhe indicava o corredor atribuído. Uma vez determinada a posição, as empilhadeiras frontais eram utilizadas para levar os paletes até os suportes colocados na extremidade do corredor de armazenamento, a fim de que as empilhadeiras trilaterais pudessem armazená-los nas localizações estabelecidas pelo sistema de gestão.
As operações de saída ocorriam de forma inversa, sendo diferente em relação à maioria dos paletes que se dirigia para as áreas de picking.
Fase 3: suprimir o transporte interno de paletes completos
O crescimento da empresa não exigia um maior número de localizações, mas sim aumentar o movimento de paletes. Visando consegui-lo, cogitou-se a possibilidade de aumentar o número de empilhadeiras e o número de operadores com o consequente risco que isso significava.
A instalação tinha quinze corredores de armazenamento e já dispunha de cinco empilhadeiras trilaterais. Embora fosse possível introduzir mais cinco, foi descartado fazê-lo uma vez que ao serem máquinas semiautomáticas e pouco rápidas, o número de ciclos oferecido era insuficiente para abranger as necessidades da Disalfarm.
Foi a partir daí que a Mecalux cogitou duas possíveis opções relacionadas com a utilização de transportadores automáticos de roletes e correntes para eliminar todos os movimentos realizados pelas empilhadeiras contrabalançadas dentro do armazém.
Primeira opção fase 3: descartada
A proposta desenhava uma cabeceira composta pelos seguintes elementos:
- Dois ramais principais perpendiculares às estantes.
- Dois circuitos (um de entrada e outro de saída) em cada um dos corredores de armazenamento.
- Posto de entrada e inspeção de paletes na área das docas com sistema de rejeição para os paletes não aptos.
- Saída direta para a expedição.
- Duas saídas para as áreas de picking.
Era a opção mais coerente do ponto de vista de proximidade às docas, assim como era válida para poder alimentar os postos de picking.
Para as operações de armazenamento seriam utilizadas as empilhadeiras trilaterais e, futuramente, se abordaria a necessidade de aumentar o número de empilhadeiras ou se encontraria uma solução automática. Além disso, a parte posterior seria destinada à área de troca de corredores para as empilhadeiras trilaterais, tal como tinha sido previsto na primeira fase.
Segunda opção fase 3: a solução
Portanto, decidiu-se que a principal parte da cabeceira ficaria localizada no lado posterior do armazém. Dessa forma, tal como já se fazia, o principal corredor seria para fazer as manobras de trocas das empilhadeiras trilaterais e circulação das empilhadeiras frontais.
Esta solução era mais complexa e cara porque implicava disponibilizar um circuito de transportadores na parte inferior de uma das estantes com a finalidade de transferir toda a mercadoria proveniente das docas. O mesmo ocorria com as saídas, mas acabou sendo a única solução que permitia sua execução sem interferir nas operações diárias.
Os movimentos entre os circuitos de entrada e as posições eram feitos através das empilhadeiras trilaterais. Quando terminou a reconstrução, o principal corredor foi disponibilizado apenas para fazer a troca de corredor das empilhadeiras trilaterais, assim como para as poucas saídas diretas realizadas para expedição.
A partir deste momento foi incorporado o programa de controle Galileo da Mecalux, responsável por dirigir todo o movimento automático dos transportadores, do posto de entradas até as saídas, passando também pela área de picking. Os terminais de radiofrequência continuaram sendo utilizados para dar instruções aos operadores das empilhadeiras trilaterais.
Fase 4: automatização total do armazém
O sucesso conseguido com a automatização dos movimentos de entrada e saída fez com que diante das novas previsões de crescimento se pensasse na possibilidade de automatizar todo o armazém.
A automatização completa trazia um novo inconveniente: as máquinas automáticas (transelevadores) existentes no mercado não permitiam deixar os paletes ao nível do piso. Para resolver tal situação a única opção viável seria que o primeiro nível tivesse uma elevação entre 60 e 70 cm do piso e que fosse colocada uma guia na parte superior dos corredores. Esta solução implicava a perda de um nível completo do armazém, ou seja, ter 1.290 paletes a menos.
Como as necessidades da Disalfarm não admitiam a perda de capacidade de armazenamento, era necessário encontrar outra via de automatização ou construir outro centro logístico.
Nessa ocasião a Mecalux lançava no mercado o transelevador trilateral, substituto natural das empilhadeiras trilaterais, que se adaptava perfeitamente às características necessárias do centro logístico da Disalfarm.
Suas peculiaridades são as seguintes:
- Pode deixar os paletes a apenas 10 cm do piso.
- Dispõe de garfos trilaterais em vez dos clássicos garfos telescópicos laterais.
- Não necessita de uma guia na parte superior dos corredores, pois só precisa de duas guias no piso.
- Sua altura máxima é de 15 m.
- Pode utilizar uma ponte de transbordo (troca de corredores).
- Também utiliza o Galileo como programa de controle.
- Consegue-se, no mínimo, a mesma capacidade obtida com as empilhadeiras trilaterais.
As modificações realizadas na fase 4
As modificações aplicadas foram mínimas e facilmente executáveis, principalmente quanto à:
- Instalar duas guias no piso.
- Modificar levemente as alturas entre níveis.
- Prolongar o posto de controle instalado sobre os transportadores da cabeceira.
- Colocar os fechamentos de segurança para que toda a instalação esteja adaptada às normas concernentes à automatização de armazéns, especialmente as relacionadas com a segurança dentro dos corredores onde operam os transelevadores.
Os acessos aos corredores relacionados com as operações de manutenção do armazém são efetuados pelo lado contrário da cabeceira, ou seja, onde ficava o principal corredor da instalação quando funcionava com as empilhadeiras trilaterais.
Para as poucas operações de saída de paletes completos foi disposto um canal dinâmico por corredor sobre os suportes que existiam na cabeceira primitiva, que pode ser acessado com empilhadeiras contrabalançadas sem necessidade de entrar nas áreas de movimentos automáticos.
Comunicação com o software
Desde o início, a Disalfarm contava com um sistema de gestão de armazéns (SGA) potente e adaptado às suas necessidades operacionais. Continuar utilizando este sistema como base de gestão de todo o armazém era uma condição obrigatória. Por isso, só foi necessário recorrer ao programa de controle padrão da Mecalux, Galileo Control System, para realizar todos os movimentos dentro do armazém.
Da mesma forma, foi desenvolvida uma interface de comunicação para que ambos os sistemas se comunicassem corretamente, assim como uma camada intermediária de gestão para evitar ordens incongruentes de reservas e ocupação de localizações.
Benefícios para a Disalfarm
- Alta capacidade de armazenamento em um espaço reduzido: o armazém da Disalfarm permite localizar 19.350 paletes de 800 x 1.200 mm.
- Melhorar sem reduzir o serviço: a Mecalux otimizou o centro logístico da Disalfarm sem que a empresa tenha deixado de trabalhar em momento algum permanecendo o tempo todo nas mesmas instalações.
- Alta produtividade: a automatização dos diferentes processos de armazenamento aumentou o fluxo de movimentos, adequando-se às necessidades da empresa.
- Controle total: a interface de comunicação entre o sistema de gestão de armazéns da Disalfarm e o programa de controle padrão da Mecalux permite gerenciar todos os processos e operações que ocorrem dentro do armazém.
Centro logístico da Disalfarm | |
---|---|
Capacidade de armazenamento: | 19.350 paletes |
Medidas do palete: | 800 x 1.200 mm |
Peso máximo do palete: | 800 kg |
Altura das estantes: | 13 m |
Comprimento das estantes: | 60 m |
Nº de transelevadores: | 15 |
Tipo de transelevador: | trilateral automático |
Galeria
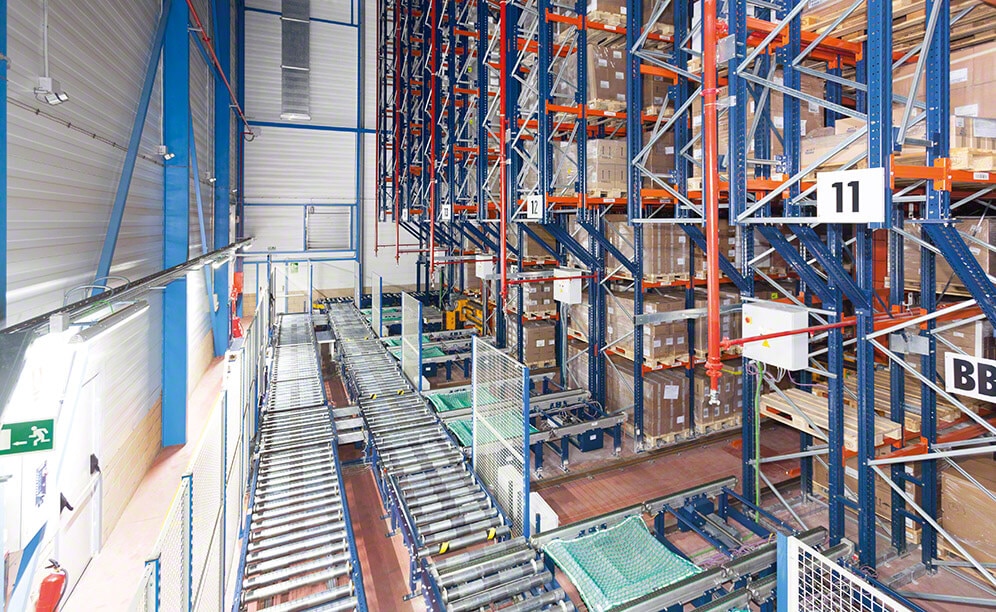
Fale com um especialista