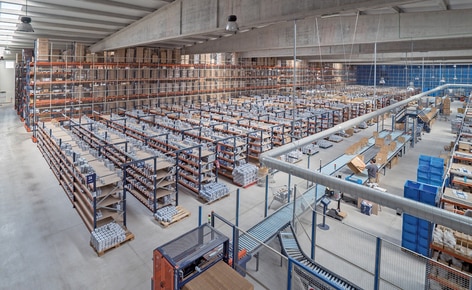
Inovação e agilidade na preparação de pedidos de venda "online" de fornecimentos industriais, ferramentas e bricolagem
Novo centro logístico de Cofan setorizado em distintas áreas com foco no picking
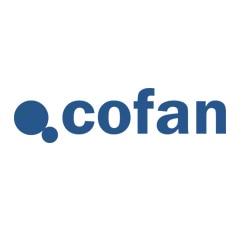
Cofan construiu um moderno centro logístico setorizado em diferentes áreas que organizam a mercadoria em função de suas características e o nível de demanda. A Mecalux forneceu todos os sistemas de armazenagem das instalações (incluído um armazém automático miniload) e um circuito de transportadores completo com estações de preparação de pedidos, formadoras de caixas, seladoras, balanças e rampas de classificação. Esta solução permite que o picking seja realizado com agilidade e de forma eficiente.
Quem é a Cofan
A Cofan é uma empresa com mais de 15 anos de experiência no desenvolvimento e venda eletrônica de produtos de fornecimento industrial, ferramentas e bricolagem. Dispõe de três marcas diferentes (Cofan, Bricofan e Cofan Home) comercializadas em mais de 12 países.
A empresa se propõe a reforçar seu ritmo de crescimento graças à inovação e à introdução da tecnologia em todos os seus processos produtivos. Atualmente a Cofan é uma referência no setor industrial e automotivo, assim como é uma marca de confiança de distribuição online.
Necessidades da Cofan
O forte crescimento registrado nos últimos anos obrigou a Cofan a construir um novo centro logístico considerando as previsões de expansão a curto e médio prazo.
A empresa precisava obter a máxima capacidade de armazenamento e classificar os produtos por tipo de referência com a finalidade de agilizar a preparação e consolidação dos pedidos. Também era necessário minimizar os custos operacionais e garantir um serviço eficiente para os usuários de seu e-commerce.
A empresa solicitou a colaboração da Mecalux para encontrar uma solução adequada que se adaptasse a todos os requisitos apresentados, permitisse aumentar o número de expedições diárias e, além disso, melhorasse os prazos de entrega dos pedidos. O projeto era um verdadeiro desafio devido à diversidade de produtos, tamanhos, pesos e classificações diferentes baseando-se nos critérios de rotatividade ABC, o que exigia uma análise muito detalhada de cada um deles.
O centro logístico
O resultado é este novo centro logístico, localizado na localidade de Campo de Criptana, a uma distância de 150 km de Madri, e muito próximo das principais plataformas logísticas da península ibérica. Situa-se em um importante ponto de ligações rodoviárias que facilita a excelente distribuição dos produtos por toda a extensão espanhola.
O armazém de 25.000 m2 está setorizado em diferentes áreas de acordo com os requisitos da empresa, o que permite classificar cada família de produtos em função de seu nível de demanda e dimensões. A operação principal é o picking, com muitos pedidos e poucas linhas de preparação para cada um deles.
Estas são as diferentes partes e setores do armazém:
- Armazém de picking manual de alto consumo
- Armazém de reserva
- Armazém de reserva e picking de produtos volumosos
- Armazém automático miniload
- Armazém de produto sensível
- Formadoras automáticas de caixas de papelão
- Circuito de transportadores e mesas de preparação
- Área de consolidação e controle
- Área de classificação de pedidos
Picking: a principal função do centro logístico
Pelas características e tipologia dos pedidos, a parte central do armazém foi destinada aos produtos de maior consumo. Nesta área era necessário dispor de uma grande acessibilidade, além de flexibilidade, com um número de operadores variável em função da demanda e da faixa horária.
Para cumprir tal objetivo, foram instaladas estantes de pouca altura com uma capacidade limitada de referências. Os paletes de reserva destes produtos se encontram nas estantes situadas em ambos os lados da área de picking e a reposição é realizada aproveitando as horas vazias, ou seja, quando há menos trabalho de preparação de pedidos.
Pelo centro desta área percorre o circuito de transportadores que se desloca a uma velocidade de 45 m/min e no qual foram dispostas, em ambos os lados, seis mesas de roletes de grande capacidade para a preparação dos pedidos.
Formadora de caixas
Todo o processo começa com a formação de caixas. Esta tarefa é realizada por quatro máquinas automáticas (cada uma delas destinada a um tamanho diferente) localizadas no começo do circuito de transporte.
O software de gestão de armazéns (SGA) comunica às formadoras a quantidade de caixas e o tamanho exigido pelos pedidos, considerando a composição de cada onda de preparação. As caixas, identificadas através da atribuição e colagem de etiqueta, se dirigem progressivamente pelo circuito de transporte até a primeira mesa de preparação, onde se encontra o produto necessário para seu pedido. O operador lê a etiqueta do pacote com um terminal de radiofrequência para conhecer o material que deve ser colocado.
Armazém de picking manual
Cada uma das seis mesas de preparação dispõe de uma área com um número determinado de estantes. Os operadores percorrem os corredores das estantes utilizando carrinhos para recolher as referências que o SGA indicou através do terminal de radiofrequência.
Uma vez finalizada esta fase, o pedido é devolvido ao transportador para ser transferido à próxima estação que dispõe dos produtos necessários. Caso tenha sido completado, o transportador o encaminha automaticamente até a área de consolidação e classificação.
Armazém automático miniload
Depois desta área de alto desempenho, se encontram as mesas de preparação adjacentes ao armazém automático de caixas miniload. Nesta área estão localizados os produtos de pouco tamanho e menor consumo (basicamente dos tipos B e C).
O consumo destes produtos cumpre o princípio 80/20 de Pareto, ou seja, 80% das referências apenas representam 20% dos movimentos do armazém.
Armazém de produto sensível
Em seguida, o circuito dirige-se às estantes de paletização convencional para depositar os produtos volumosos e de menor demanda. Exatamente ao lado, o armazém de produto sensível constitui a última fase do circuito.
Finalização
Os pedidos completados são transferidos para a área de consolidação para serem embalados, etiquetados e emitida a documentação necessária para sua expedição.
Considerando as necessidades da empresa, e devido à grande quantidade de pedidos despachados por jornada de trabalho, para esta área foram previstos dois conjuntos de balanças, seladoras e etiquetadoras totalmente automáticas. Depois de passarem pela área de consolidação, os pedidos terminados são encaminhados para as cinco rampas de classificação localizadas na frente das docas de carga. Ali são agrupados por rotas e agências antes de serem expedidos.
Armazém miniload
No armazém automático para caixas são alojados os produtos de menor tamanho e baixa rotatividade. Nesta área do centro logístico, onde se realiza a preparação de pedidos de acordo com o princípio de “produto ao homem”, foram instalados dispositivos put-to-light que agilizam a operação e minimizam os erros da gestão manual.
Há dois postos de picking onde os operadores recebem as caixas provenientes do armazém e, nas suas costas, uma mesa de preparação de pedidos com capacidade para ondas de onze pedidos ao mesmo tempo.
Os transelevadores colocam os contêineres (eurocaixas) com a mercadoria nos transportadores, que se encarrega de levá-los automaticamente aos postos de picking. Os operadores extraem os produtos indicados pelo sistema através de uma tela e passam a depositá-los na caixa de papelão correspondente na mesa de preparação de pedidos.
Os monitores put-to-light guiam visualmente os operadores através de três cores diferentes, que lhes assinalam onde devem deixar cada artigo. O operador clica no indicador para confirmar que a ação foi executada.
O armazém automático é composto por três corredores com estantes de profundidade simples em ambos os lados. As estantes dispõem de 19 níveis, que alcançam uma altura de 8,6 m.
Por cada corredor circula um transelevador miniload de tipo monocoluna que se encarrega de gerenciar as entradas e saídas da mercadoria. Estas máquinas trabalham a uma velocidade de translação de 180 m/min e 100 m/min em elevação.
O transelevador está equipado com um sistema de extração de pás, que se introduz pela parte inferior das caixas para extraí-las ou situá-las nas localizações de ambos os lados do corredor.
Na parte posterior dos corredores foi disponibilizada uma área de manutenção com portas de acesso seguro que zelam pela segurança dos operadores. Os transelevadores se dirigem para esta área quando precisam de alguma intervenção ou conserto.
Easy WMS da Mecalux
O armazém de picking automático é gerenciado pelo software de gestão de armazéns Easy WMS da Mecalux, que se encarrega de controlar e coordenar seu correto funcionamento.
Este potente sistema realiza diferentes operações, entre as quais se incluem a atribuição de localizações e armazenamento das caixas de acordo com sua rotatividade, extração da mercadoria e preparação de pedidos.
O Easy WMS da Mecalux está em comunicação permanente e bidirecional com o SGA geral do armazém e o ERP da Cofan, transferindo dados e informações para conseguir a máxima produtividade e rentabilidade do picking.
Diferentes sistemas de armazenagem
A distribuição dos diferentes sistemas de armazenagem instalados no centro logístico se ajustam à grande variedade de produtos disponíveis considerando sua demanda e rotatividade, o que permite agilizar a preparação de pedidos.
Na parte central, onde são alojados os produtos de maior consumo e menor tamanho, foram instaladas 59 estantes de picking de 2,5 m de altura e 2,7 m de comprimento. São formadas por três e cinco níveis com prateleiras.
Os corredores dispõem da largura suficiente para que os operadores circulem com agilidade e sem interferências. Um terminal de radiofrequência conectado ao SGA do armazém permite identificar e classificar os produtos. Os pedidos são preparados por ondas, ou seja, vários pedidos ao mesmo tempo com a finalidade de otimizar ao máximo o percurso ao longo das localizações dentro das instalações.
Ao redor da área destinada ao picking manual de grande consumo foram instaladas estantes de paletização convencional de 7,5 m de altura. Nelas são armazenadas a mercadoria de grande volume e a reserva dos produtos de alta rotatividade em paletes. Também se efetua picking diretamente sobre os níveis inferiores.
Os operadores utilizam preparadoras de pedidos de cota baixa, uma vez que estão adaptadas para fazer picking em uma posição ergonômica e podem transferir até dois paletes ao mesmo tempo.
Foi disponibilizada uma passagem inferior que cruza de forma transversal as estantes e cumpre a função de saída de emergência, além de facilitar o fluxo da mercadoria. Os módulos da parte superior da passagem de segurança estão com telas de proteção para evitar a queda de materiais.
Benefícios para a Cofan
- Alta capacidade de armazenamento: o novo centro logístico de 25.000 m2 da Cofan está equipado com diferentes sistemas de armazenagem que se adaptam à sua ampla variedade de produtos, com dimensões muito distintas.
- Eficiente sistema de preparação de pedidos: a distribuição da mercadoria, considerando suas características e demanda, permite otimizar os movimentos dos operadores e rentabilizar ao máximo a preparação de pedidos.
- Gestão eficiente: a combinação dos diferentes softwares que intervêm nas instalações, tanto de gestão quanto de controle, juntamente com o ERP da Cofan, tiram o máximo partido de todos os recursos.
Armazém automático miniload Cofan, Espanha | |
---|---|
Capacidade de armazenamento: | 14.334 caixas |
Peso máximo por caixa: | 30 kg |
Número de transelevadores: | 3 |
Altura do armazém: | 8,6 m |
Níveis de armazenamento: | 19 |
Postos de picking: | 2 |
Galeria
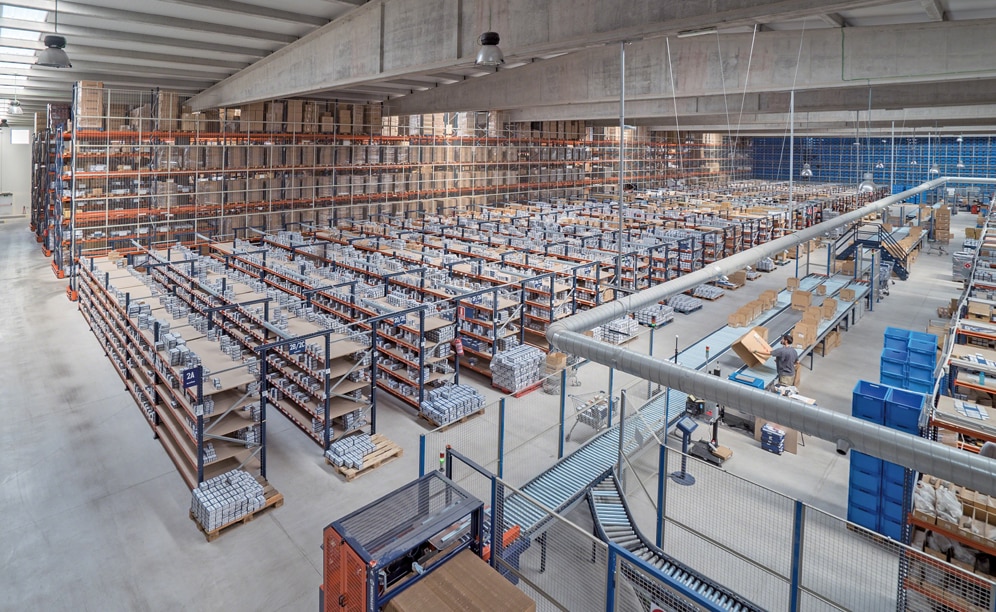
Fale com um especialista