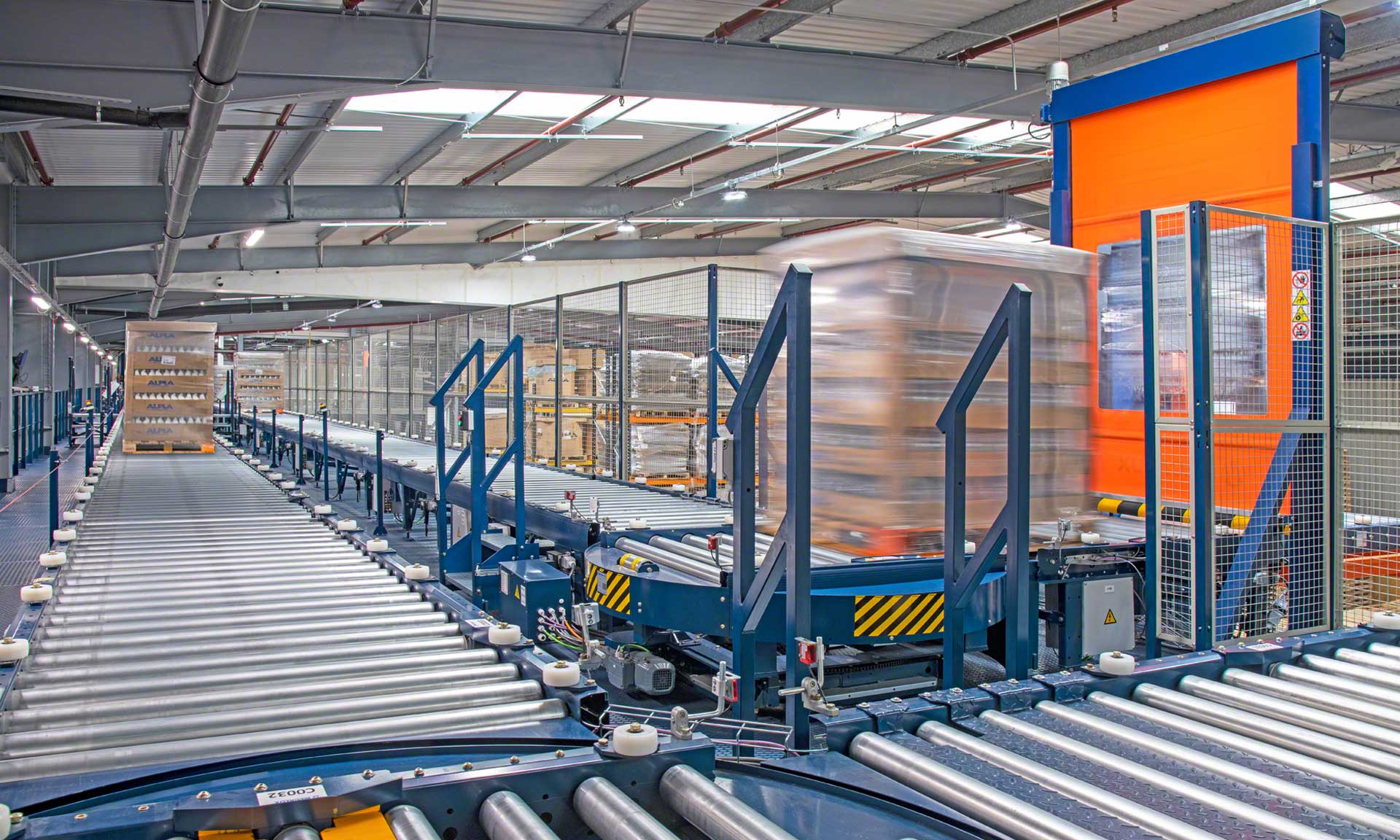
ALPLA instala um sistema de transporte automático na fábrica de Golborne (Reino Unido)
ALPLA, líder mundial no desenvolvimento e fabricação de sistemas de embalagem plástica, move 2.500 paletes diários graças a um sistema de transportadores automáticos.
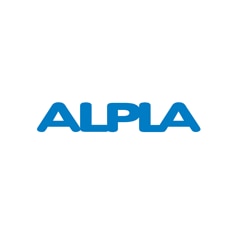
ALPLA instalou um circuito de transportadores automáticos para conectar o armazém com as linhas de produção em seu centro em Golborne. O líder mundial em desenvolvimento e fabricação de sistemas de embalagem plástica pode mover 2.500 paletes todos os dias graças a um sistema de transporte automático.
ALPLA: soluções de embalagem inovadoras
Fundada na Áustria, a ALPLA é uma das empresas líderes mundiais na área de soluções de embalagem. A empresa é reconhecida em todo o mundo por produzir embalagens plásticas da mais alta qualidade. Seus recipientes e embalagens plásticas são utilizados em uma ampla gama de indústrias, como alimentícia, farmacêutica ou cosmética. A prioridade da empresa é desenvolver uma atividade sustentável e amiga do ambiente graças às suas próprias instalações de reciclagem.
- Ano de fundação: 1955
- Presença internacional: 45 países
- Centros de produção: 177
- Equipe profissional: 22.100
- Volume de negócios: 4.000 milhões de euros em 2021
DESAFIOS
|
SOLUÇÕES
|
BENEFÍCIOS
|
---|
Como um armazém pode ser conectado automaticamente à planta de produção quando há uma separação de 70 m e uma estrada entre os dois prédios? ALPLA, uma das empresas líderes em soluções de embalagem, conseguiu responder a este desafio com uma solução tecnológica da Mecalux. “Com a solução logística instalada, composta por transportadores e elevadores automáticos de paletes, reduzimos drasticamente nossos custos de manuseio e emissões de dióxido de carbono, realizando uma atividade mais sustentável e ecológica”, explica Liam Grimwood, diretor de engenharia da fábrica do Reino Unido de ALPLA.
ALPLA, presente em 45 países, atingiu quatro mil milhões de euros em faturação em 2021, mais 8,4% que no ano anterior. No Reino Unido, a empresa está realizando um plano de crescimento inédito e, há alguns anos, conta com uma moderna planta de produção na cidade de Golborne.
O complexo logístico é composto por dois edifícios, um para as linhas de produção e outro para a área de armazenamento, separados por uma via pública. “Antes, dependíamos muito do uso de veículos pesados para transportar manualmente as mercadorias do centro de produção para o armazém”, comenta Grimwood.
À medida que o volume de produção aumentava, também aumentavam os deslocamentos e a movimentação de caminhões entre os prédios de produção e armazenamento de ALPLA. Chegou um ponto em que a transferência manual de mercadorias se tornou insustentável. “Precisávamos de um sistema para comunicar os dois prédios e mover automaticamente a mercadoria da planta de produção para o armazém. Queríamos deixar de lado o manuseio manual e o uso de veículos pesados”, reconhece o diretor de engenharia da planta do Reino Unido de ALPLA.
A solução para as necessidades da ALPLA foi a construção de um túnel elevado, com oito metros de altura, que atravessa a via pública para ligar a unidade de produção e a área de armazenamento. “Escolhemos a Mecalux por sua experiência anterior na realização de projetos como o nosso. A experiência e o conhecimento da equipe técnica e do gerente de projeto, que nos acompanharam e aconselharam em todos os momentos, também foram fundamentais na sua escolha”, reconhece Grimwood.
Comunicação através de sistemas automáticos
"Cada dia movimentamos cerca de 2.500 paletes graças a um sistema de transporte automático que funciona 24 horas, sete dias por semana", comemora Grimwood.
O sistema instalado pela Mecalux é composto por um duplo circuito de transportadores, que movimentam a mercadoria desde a produção até o armazém. “Sua principal função é transportar paletes com bandejas de papelão contendo garrafas vazias, caixas e recipientes metálicos com pré-formas de polietileno tereftalato”, explica o diretor de engenharia da planta do Reino Unido de ALPLA. No futuro, a solução escolhida poderia transportar até 5.000 paletes diários, ou seja, ALPLA duplicaria o número de movimentos entre a planta de produção e o armazém.
Os transportadores são um sistema automático de transporte de mercadorias composto por uma bateria de roletes que suportam a carga e a impulsionam ao longo do circuito. O sistema possui motores elétricos que movimentam as unidades de carga de forma controlada e segura. Os transportadores de roletes permitem economizar tempo e ganhar eficiência naquelas transferências de cargas repetitivas e com circuitos já definidos.
Além dos transportadores, foram instalados sete elevadores automáticos que movimentam os paletes na vertical. Os elevadores permitem colmatar a diferença de nível entre o circuito de transporte ao nível do solo e o túnel elevado. Desta forma, os paletes podem fazer todo o trajeto desde a planta de produção até o armazém de forma totalmente robótica.
No início do circuito de transporte e exatamente onde os paletes saem das linhas de produção, foi instalada uma estação de inspeção (PIE). Este sistema automatizado de medição de paletes e controle de qualidade é essencial para garantir que tanto a mercadoria quanto os paletes que entram no circuito de transporte sejam adequados para circulação e não causem nenhum tipo de acidente. O posto de inspeção verifica se as dimensões, peso e condição dos paletes atendem às especificações da instalação.
Principais componentes dos transportadores de roletes
- Roletes. Cilindros de metal que incluem um eixo e dois rolamentos. Colocados um após o outro, são eles que suportam o peso do palete e o deslocam até o final do percurso.
- Estrutura e pés metálicos. Eles formam o suporte para os roletes e são feitos de diferentes tipos de aço, dependendo do peso que têm de suportar. Sua função: marcar a direção do circuito dos transportadores.
- Componentes elétricos. A movimentação de cargas no circuito é acionada através de um conjunto de componentes elétricos, assim como os motores e caixas de força. A potência necessária dependerá da velocidade necessária e do peso das cargas a serem movimentadas.
- Elementos de segurança. Dispositivos mecânicos ou sensores, como batentes ou fotocélulas de detecção, garantem a segurança da instalação. Além disso, permitem saber a todo o momento onde se encontra a carga e comunicar esta informação ao software de controle.
Logística de produção eficiente
“A ALPLA de Golborne está em uma posição forte e tem a oportunidade de crescer ainda mais”, afirma Grimwood. Para continuar consolidando sua presença no mercado britânico, a empresa promove a metodologia lean em sua logística, que consiste em promover atividades que agreguem valor ao negócio para aumentar o fluxo de produtos e minimizar custos.
A solução da Mecalux permitiu à ALPLA ter uma logística eficiente e conectada à produção através de sistemas de transporte automáticos. Atualmente, a indústria exige um sistema de fabricação flexível e diversificado, em que oferecer um atendimento eficiente ao cliente depende do correto direcionamento da logística de produção. Graças à solução instalada, a cadeia de suprimentos da ALPLA está mais eficiente, otimizada e preparada para enfrentar os desafios de hoje e de amanhã.
Graças à solução de transporte automático, instalada pela Mecalux, reduzimos custos e emissões de CO2, além de podermos transportar cerca de 2.500 paletes diários, 24 horas, sete dias por semana.
Galeria
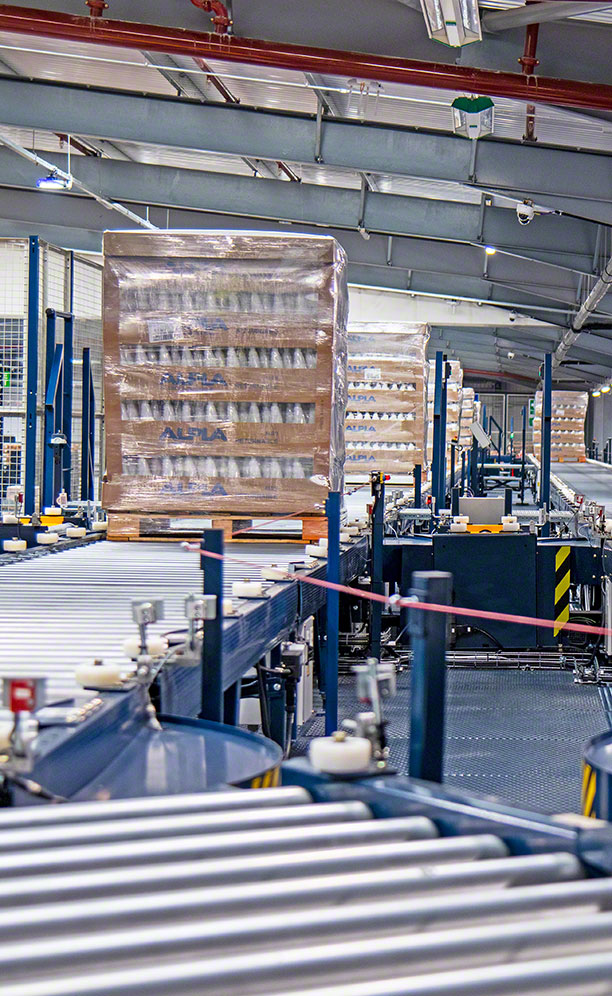
Transportadores automáticos de paletes no centro logístico de ALPLA
Fale com um especialista