Nos armazéns pequenos, poucas vezes os sistemas de armazenagem são misturados, mas quanto maior for uma instalação e maior variedade de produto for manuseada, a combinação de diferentes soluções torna-se mais frequente. Com relação a esse tema, no artigo "Diferenças de capacidades entre sistemas" é possível encontrar casos em que se combinavam estantes convencionais e compactas, além de serem explicados os critérios aplicados para decidir quando utilizar uma ou outra configuração.
No entanto, quando se trata de armazéns médios e grandes, as combinações não se limitam às estantes compactas e convencionais, mas também é habitual misturá-las com outras soluções específicas para picking, assim como estas últimas entre si. De fato, a combinação de sistemas de armazenagem de caixas ou produtos soltos, utilizando conjuntamente as duas modalidades do homem ao produto e o produto ao homem, vai ser cada vez mais usual no futuro. Cada sistema tem sua aplicação adequada em casos específicos e o segredo é saber combiná-los corretamente.
O que se pretende, quando se busca a solução adequada, é tratar cada produto de forma individual e, posteriormente, agrupá-lo com outros em função dos critérios de rotação (A-B-C) e das famílias às quais pertencem, a forma de preparar os pedidos e o tamanho dos produtos. Todos estes dados podem ser extraídos através da análise que se denomina mestre de artigos. Graças a isto, é possível conhecer, por exemplo, a conveniência ou não de estabelecer diferentes zonas ou diferentes operações (ou ambas), em cujo caso será necessário prever a necessidade de delimitar uma área de consolidação de pedidos.
A seguir, expomos vários exemplos de combinação de sistemas, que proporcionarão uma ideia das variadas e possíveis configurações (as quais são, praticamente, ilimitadas).
Exemplo 1. Picking unitário |
|
Neste caso existem quatro áreas definidas e as operações são gerenciadas mediante um WMS. Os produtos de alto consumo são alojados em estantes dinâmicas de picking equipadas com em style="background-color: transparent;">pick to light (identificadas com o número 1 na imagem superior). Os produtos de consumo médio são alocados em três carrosséis horizontais (número 2), enquanto os produtos de baixo consumo se encontram armazenados em estantes clássicas colocadas sobre um mezanino (número 3). A quarta zona (número 4) destina-se à consolidação, assim como é a área para onde as encomendas ou os pedidos preparados são enviados às demais zonas. As diferentes áreas de preparação estão interligadas à de consolidação por um sistema de transportadores automáticos para caixas. Graças a esta configuração, a área que fica debaixo do mezanino (dotada com um elevador para interligá-la ao sistema de transporte automático) está disponível para depositar a mercadoria que está pronta para sua expedição. |
Exemplo 2. Picking unitário altamente automatizado |
|
Este tipo de instalação é desenvolvida, cada vez com mais frequência, uma vez que permitem reduzir os custos de exploração. Consiste em uma solução totalmente integrada. Em cada zona foi escolhido o sistema de armazenagem, preparação e manutenção mais apropriado para cada produto. Portanto as diferentes operações realizadas no armazém conseguem ser otimizadas ao máximo. Foi instalado um sistema de transporte interno, totalmente automatizado, que interliga as diferentes áreas, o que significa não ter que destinar pessoal e equipamentos de manutenção para esta tarefa. Graças a este sistema de transporte, os pedidos são classificados, automaticamente, por rotas e destinos Em instalações desta complexidade é fundamental dispor de um sistema de gestão (WMS) apropriado que se encarregue de controlar toda a operação. |
Exemplo 3. Armazém de paletes e miniload |
Neste exemplo, o miniload está situado dentro de um armazém de paletes de produtos de tamanho médio e grande com muitos acessórios de consumo variado. Para o picking foram estabelecidas quatro áreas com diferentes processos.
Todo o sistema funciona ao mesmo tempo, como uma unidade de trabalho. Quando os pedidos são lançados, agrupados por remessas, a primeira atividade realizada pelos operadores é a preparação das caixas completas e sua colocação sobre os transportadores para serem conduzidos até a zona de consolidação. Uma vez realizada esta fase, o pessoal prepara os acessórios soltos de médio e alto consumo que são introduzidos por eles em contêineres. Os pedidos que forem completados nessa fase se deslocam, mediante transportadores, até a área de consolidação, aqueles que não tenham sido completados, se dirigem à cabeceira do miniload para que um operador adicione o produto que falta ao contêiner e, uma vez que o pedido esteja fechado, o contêiner será levado até a área de consolidação O resto do armazém funciona por áreas independentes e o produto preparado é consolidado nas próprias docas. Além disso, o sistema de gestão é capaz de desagregar e gerenciar todos os pedidos e todas as zonas.
|
Exemplo 4. Solução para uma câmara de congelamento |
Este hipotético armazém compõe-se de estantes dinâmicas de paletes para produtos de alto consumo e exigências de rotação. Também se alocam estantes convencionais sobre bases móveis destinadas a produtos de rotação B e C (com o nível inferior dedicado a tarefas de picking de caixas individuais). Da mesma forma, há outras estantes convencionais que também se dedicam a produtos de rotação B e C, mas ao contrário das anteriores, estas são estáticas, pois foram colocadas para aproveitar os espaços irregulares da instalação. Todas estas áreas contam com o apoio de transportadores automáticos que, além de se encarregarem do movimento da mercadoria fora das estantes, servem como um buffer de pedidos preparados, para o qual foi instalado um grupo deles perto das docas. A preparação de pedidos é realizada mediante equipamentos de radiofrequência ou através de um sistema de picking por voz. Esta segunda opção é mais apropriada para uma câmara de congelamento, visto que os operários ficam com as mãos livres.
|
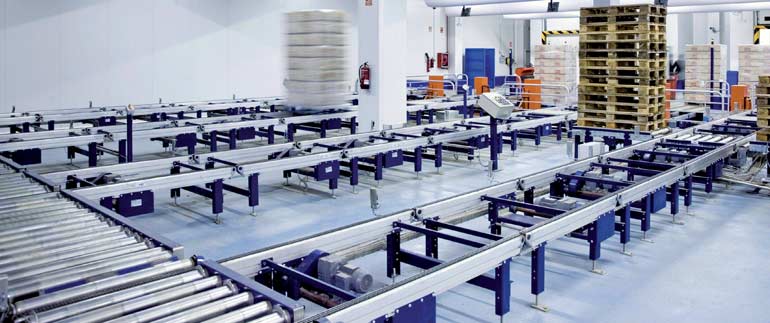
Armazém para empresa produtora e distribuidora de pão pré-cozido, produtos de panificação congelados e doces
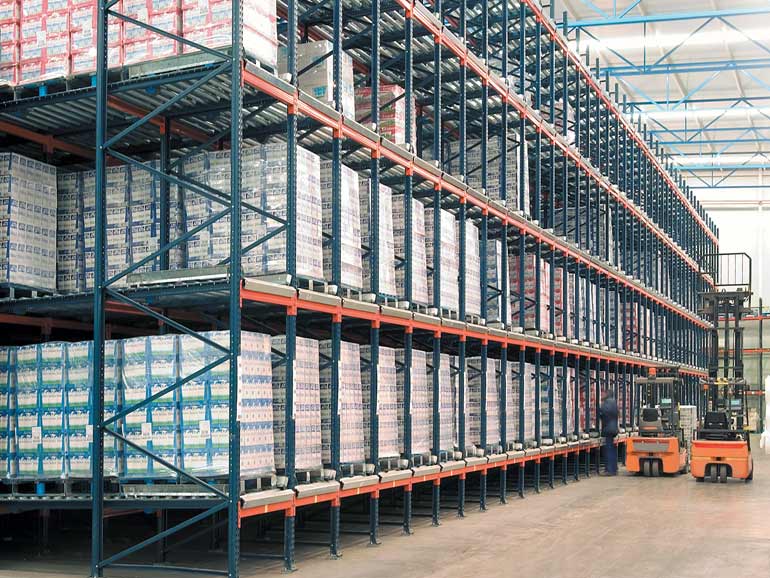
Armazém para corporação dedicada ao setor alimentício
Exemplo 5. Paletização e picking |
|
No armazém automático de paletes, com quatro transelevadores, são armazenadas principalmente as reservas dos produtos de consumo médio e a mercadoria volumosa. Na zona externa dispõe-se de um mezanino com transportadores e postos de picking para preparar pedidos diretamente sobre os próprios paletes. O operador dispõe de ferramentas de ajuda, sobretudo meios informáticos e leitores de código de barras, que além de facilitar as operações de picking permitem repor a mercadoria destinada ao armazém de caixas miniload. No armazém convencional para produtos paletizados são armazenados os produtos de pouco consumo de tamanho médio e medidas irregulares, são utilizadas empilhadeiras trilaterais e máquinas selecionadoras de pedido ou encomenda de cota alta para efetuar o picking diretamente sobre as estantes. Nas estantes compactas são depositados os produtos de grande consumo, que em geral são enviados em paletes completos. Para sua manipulação são utilizadas empilhadeiras retráteis O armazém automático de caixas, com nove miniloads, armazenam em caixas os produtos de pequenas e médias dimensões. Três níveis de transportadores atendem os postos de picking: o nível inferior transfere as caixas da cabeceira de cada corredor aos diferentes postos de picking e a o transportador que conduz á área de reposição; o nível intermediário é utilizado para o retorno e as entradas das caixas no armazém; o nível superior envia as caixas com pedidos preparados até o sorter de classificação. O uso dos três níveis evita interferências e facilita o fluxo das caixas. Os postos de picking foram ergonomicamente concebidos para facilitar a preparação dos pedidos e evitar tempos mortos. Nos armazéns verticais são guardados componentes e produtos delicados ou de grande valor e tamanho pequeno. Na parte inferior do mezanino, os transportadores são interligados mediante elevadores com os da parte superior, tanto os de paletes quanto os de caixas, podendo realizar as seguintes operações:
O circuito de transportadores de roletes e correias aéreas, de dois níveis, interliga os dois armazéns automáticos e também permite trasportar os pedidos preparados ao sorter de classificação. Os pedidos já preparados provenientes do sorter são consolidados, por rotas com os do armazém convencional e os paletes completos do armazém automático, diretamente em áreas colocadas em frente das docas de expedição. Para o transporte dos paletes na zona de recebimento e expedição, são utilizadas transpaletes elétricas e manuais
|